This year, EREM is celebrating 25 years in the business of high added-value motors. Provider of motor breakdown solutions and manufacturer of sub-assemblies, EREM supplies spare parts, performs repairs, together with designing brand new and specially-adapted motors. EREM is also celebrating their 20 years of experience in making spindles to precise technical specification standards. EREM has forged a solid and enduring partnership over the years with SIEMENS. EREM is today the sole French company certified by SIEMENS to carry out repairs on their servomotors.
Leader in high-tech expertise and solutions with corresponding high-tech plant and machinery, EREM is far from the image of a simple winding shop!
EREM have been honing their expertise over the past twenty years, responding to the demands of SIEMENS clientele who require diverse specifications of their special DC motors (see box). Firmly implanted in the Oise region of France, at the intersection of Amiens, Beauvais and Compiegne, the company, with its 23 employees, promote a joint strategy: to guarantee a reactive service to meet all possible challenges and to devise turnkey spindles as defined in specific technical specifications. In 2016, EREM add a 1,000 m² extension to their existing premises of 2200 m.
20 years of experience
“we first worked to a precise technical specification standard back in 1996, recalls the founder and owner of EREM, Paul Maier; we created an extremely detailed prototype in order to understand the complexities of the product down to its finest of details. This enabled us to work alongside Siemens to provide technical support to their client base. Empowered by this knowledge and experience, in 1998 we created and produced our first spindles. We went forward with this line of activity to develop our business alongside Siemens, without ever having to compete with the other usual spindle manufacturers”.
Designing to Precise Technical Specification Standards
EREM only responds to non-catalogue orders, like for special operating conditions, a restrictive set-up, or orders under very tight deadlines. We work according to the statement of work right from the initial assistance through to the delivery of the result-guaranteed turnkey motor.” EREM commits right from the preliminary schedule through to the final study of the project.” We are indeed willing to perform qualification testing as demanded by clients.” EREM possesses their own internal machine centre used as testbed to simulate spindles, for example, in real and identical conditions as those of clients.
“This enables us to apprehend the different kinds of problems that our clients may come across and in this way we can show them why and how we were able to solve these problems.
Any size and any field
EREM undertake spindle projects of varying sizes from 3kw to several hundred kw’s. “We have, for example had to produce 200 kw spindles, rotating at 20,000 rpm” affirms Paul Maier. EREM also do not hesitate to undertake projects involving high-torque systems.
In respects to upgrading and “retrofitting”, and following the client’s requirements, the specialist company is able to work on older machines in order to either repair or completely overhaul the existing spindle whilst preserving the original interfaces.
Included amongst the category of truly “special” development projects, Paul Maier never tires of recalling one of his more original projects: “ for a very large boring machine, equipped with a low speed spindle, we designed and produced a smaller spindle to fit into the original spindle; the latter’s rotation was stopped whilst the smaller spindle was in use, thus enabling the client to perform faster machining with the adaption of a smaller spindle, hence a saving of overall production time.
In general terms, EREM, offer to design and produce spindles in order to fully optimise a machine’s original use.
Spindle Repair
Manufacturer of bespoke spindles, EREM also undertake the repair of subassemblies : “This is where our technical and design expertise come to light, in our ability to improve on the performance of the spindle”.
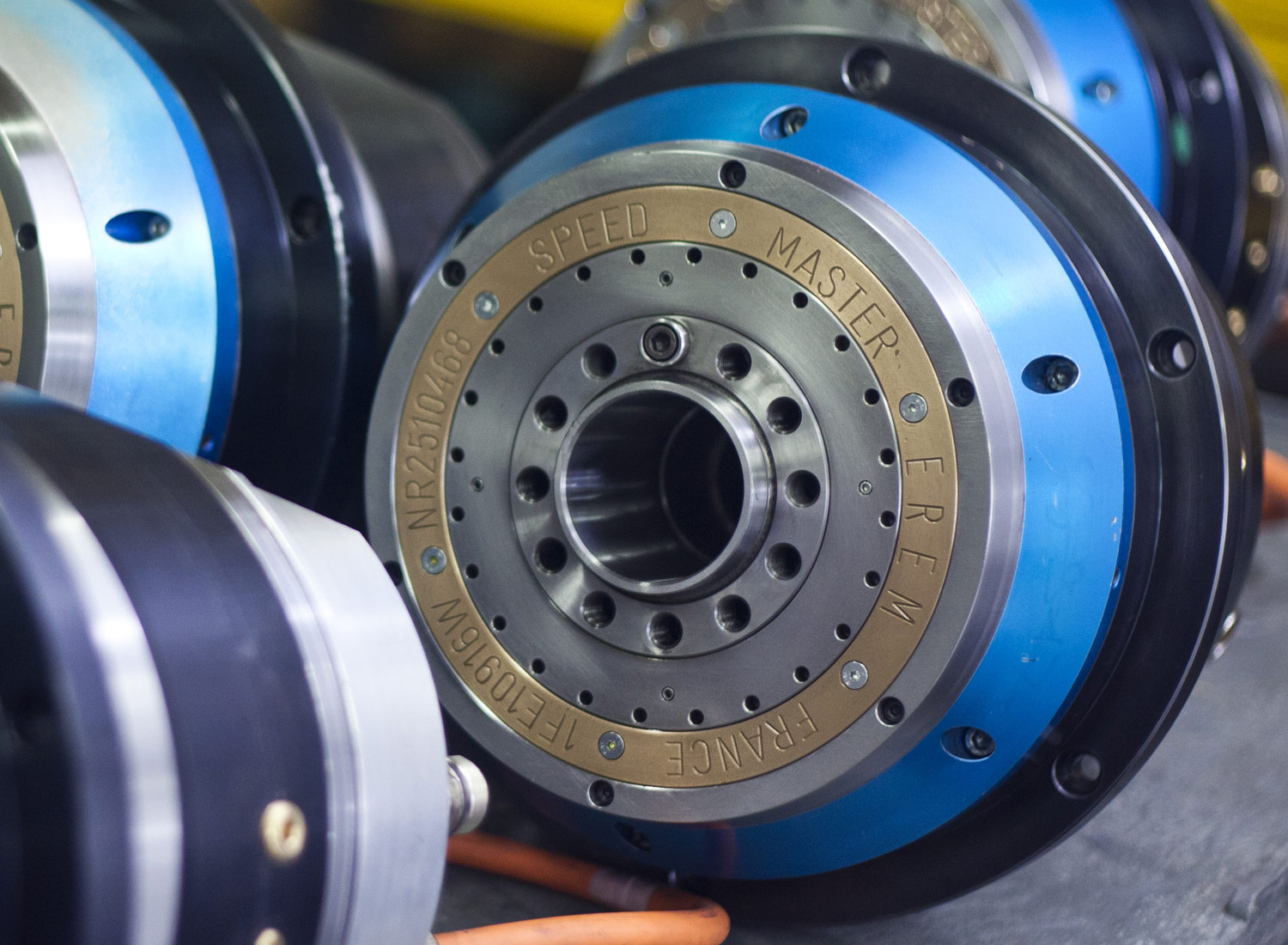
Beyond the motor…
Paul Maier founded EREM in 1991, an enterprise specialising in high added-value repaired motors. His trump card: high technical prowess. As early as 1993, EREM became the sole certified motor repair company for SIEMENS. The company masters both electrical and mechanical drive systems (bearings, shafts, flanges…); provider of total project management solutions. “During the first 10 years of our collaboration with SIEMENS, we developed 5 to 60kw DC motors. From the semi-finished parts we had in stock, we performed the assembly, necessary machining, and final tasks under very tight deadlines of 3 to 4 days! This is how we started our manufacturing business.”
Nowadays, EREM’s business activity is made up of three equal branches, namely, motor winding, designing and manufacturing new spindles, and the repair of existing spindles. Each year, 150 to 200 spindles pass through the workshop for maintenance and repair.
EREM: A company committed to R&D
The company has also initiated a research & development programme alongside the Jules Verne University of Picardy, ESIEE of Amiens, and the technology transfer platform, Innovaltech. A programme involving a consortium of several industrial companies (notably in the sector of transmission systems for farm tractors). “In this context, a doctoral candidate within the company has been preparing her CIFRE thesis since October 2015,” reveals Paul Maier. The topic: developing electrical energy transfer in complex mechanical systems.”
Objective: To quantify the effort of the ball on the ring and so the stress in the bearing, in order to obtain instant information without hysteresis.
In addition, EREM possess an internal machining workshop as well as a full range of CN machine tools, and a machining centre used as a testbed. Spindle tests are thus performed by simulating the actual conditions to those of the clients. “This means we can apprehend problems that clients may subsequently come across, which enables us to show them why, and how, we have been able to solve these problems”.